在工业领域,大型生产活动对稳定环境条件的依赖程度极高,温度、湿度等环境因素的细微波动,都可能对生产流程、产品质量产生重大影响。传统空调系统在满足这些环境需求时,能耗巨大,成为企业运营成本的沉重负担。而工业省电空调的诞生,犹如一场变革的春风,以其微小能耗,为大型生产注入了强大的变革动力,重塑着工业生产的格局。
一、传统空调能耗与大型生产需求的矛盾
大型生产车间往往面积广阔,设备众多且运行功率大,产热量惊人。传统空调为维持适宜的生产环境,需持续高负荷运转。据不完全统计,在汽车制造、钢铁冶炼等行业,传统工业空调系统的能耗占企业总能耗的 35% - 45%。以一家拥有 5 万平方米生产车间的汽车制造工厂为例,夏季高温时段,为确保焊接、涂装等工艺不受高温影响,数十台传统大功率空调全天 24 小时不间断运行,每月电费高达上百万元。而且,传统空调的制冷制热效率有限,在应对车间复杂多变的热负荷时,常常出现过度制冷或制热现象,不仅浪费能源,还难以精准维持环境参数,影响产品质量与生产效率。例如在电子芯片制造车间,温度偏差超过 ±1℃,就可能导致芯片良品率大幅下降,给企业带来巨大经济损失。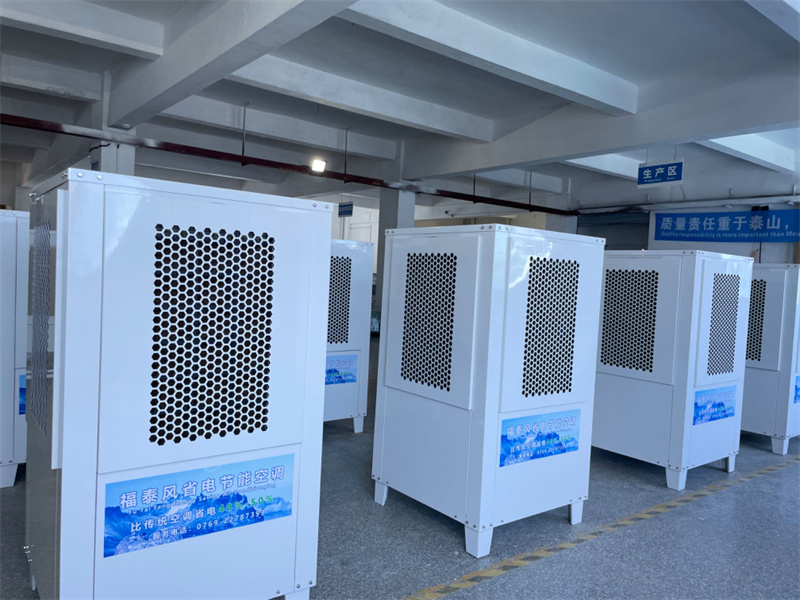
二、工业省电空调的节能技术解析
工业省电空调采用了先进的高效压缩机技术,其内部结构经过优化设计,减少了机械摩擦损耗。同时,搭载智能变频控制系统,可根据车间实际热负荷实时调整压缩机转速。当车间生产设备部分停机或夜间生产负荷降低时,压缩机自动降低转速,减少制冷量输出,能耗随之大幅降低。例如在某大型电子元器件生产车间,应用高效压缩机技术的省电空调,相较于传统定频压缩机空调,能耗降低了约 30%。在负荷高峰期,压缩机又能迅速提升转速,高效制冷,满足车间对环境温度的严格要求。
智能控制系统是工业省电空调的核心 “大脑”。通过在车间各个区域安装大量温湿度传感器、人员活动传感器以及设备运行状态传感器,实时收集环境数据。这些数据被迅速传输至中央控制系统,系统依据预设的最佳环境参数以及车间实际工况,智能调控空调的运行模式。比如在午休时间,车间人员减少、设备部分停机,系统自动将空调切换至低功率运行模式,仅维持必要的环境温湿度条件,避免了不必要的能源消耗。与传统手动或简单定时控制的空调相比,智能控制的工业省电空调能耗可降低 20% - 30%,且能将车间环境参数精准控制在极小范围内,为大型生产提供了稳定可靠的环境保障。
工业省电空调在热交换技术方面实现了重大突破。采用特殊材料制造的热交换器,具有超高的热传导效率。在制冷过程中,能快速将车间内的热量转移至室外,缩短制冷时间,降低压缩机运行时长,从而减少能耗。制热时,高效收集室外热量用于室内供暖,相较于传统热交换器,制热效率提升了约 25%。部分高端工业省电空调还配备了热回收装置,将制冷过程中产生的废热进行回收利用,可用于加热生产用水或为车间局部区域供暖,实现了能源的二次利用,进一步降低了整体能耗。
三、工业省电空调驱动大型生产变革的实例
某大型汽车制造企业,拥有多个大型生产车间,以往传统空调系统能耗巨大,且车间环境稳定性欠佳,影响了汽车零部件的装配精度和整车质量。引入工业省电空调后,能耗显著降低。经统计,夏季制冷高峰期每月电费节省了约 40 万元,降幅超 30%。同时,车间温度波动控制在 ±0.5℃以内,湿度控制在理想范围内,汽车零部件装配精度提高,次品率降低了约 15%,生产效率因环境稳定提升了约 12%,企业经济效益与产品质量得到了双重提升。
一家大型食品加工企业,生产车间对温度、湿度要求极为严格,以保证食品的安全与品质。原有的传统空调系统不仅能耗高,而且温湿度控制精度不足,导致部分食品出现变质、口感变差等问题。换装工业省电空调后,每月电费降低了约 20 万元,降幅达 28%。车间温湿度稳定性大幅提升,食品变质率降低了约 20%,产品品质得到了有效保障,企业市场竞争力进一步增强。
工业省电空调凭借其先进的节能技术,以微小能耗驱动着大型生产在成本控制、产品质量和生产效率等方面实现了重大变革。随着技术的不断创新与完善,工业省电空调必将在更多大型生产领域发挥关键作用,成为推动工业可持续发展的重要力量。